What is FDM?
Fused Deposition Modeling Explained13
MAY, 2019
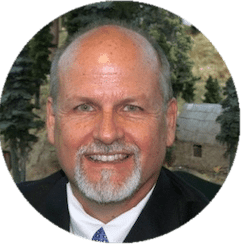
Paul Cesak
There are quite a number of 3D printing methods. Perhaps the most widely used is FDM, or Fused Deposition Modeling. This method uses a continuous filament made of thermoplastic which is heated to its melting point and extruded and deposited and fused, layer by layer, to create the desired model. This process was created by Scott Crump, the founder of Stratasys, back in 1988.
How Does FDM work?
Any 3D print initially starts out as a CAD (Computer Aided Design) file. The CAD file is then converted to a format the 3D printer can understand, typically an OBJ or STL format, although there are other formats.
FDM printers use two types of materials, a modeling material, which becomes the completed item, and a support material, which supports the item being printed and is removed afterwards.
During the printing process, these materials are extruded as plastic threads, or filaments, which unwind from a coil and are then fed through the extruder nozzle. The nozzle melts the filaments and extrudes them onto a base, sometimes called a build platform, bed or table. Both the nozzle and the base are controlled by the computer that translates the dimensions of an object into X, Y and Z coordinates for the nozzle and base to follow during the printing.
In a typical FDM system, the extrusion nozzle moves over the build platform horizontally and vertically, “drawing” a cross section of an object onto the platform. This thin layer of plastic cools and hardens, immediately binding to the layer beneath it. Once a layer is completed, the base is lowered — usually by about one-sixteenth of an inch — to make room for the next layer of plastic.
Printing time depends on the size of the object being manufactured. Small objects — just a few cubic inches — and tall, thin objects print quickly, while larger, more geometrically complex objects take longer to print. Compared to other 3D printing methods, such as stereolithography (SLA) or selective laser sintering (SLS), FDM is a fairly slow process.
Once an object comes off the FDM printer, its support materials are removed either by soaking the object in a water and detergent solution or, in the case of thermoplastic supports, snapping the support material off by hand. Objects may also be sanded, milled, painted or plated to improve their function and appearance.
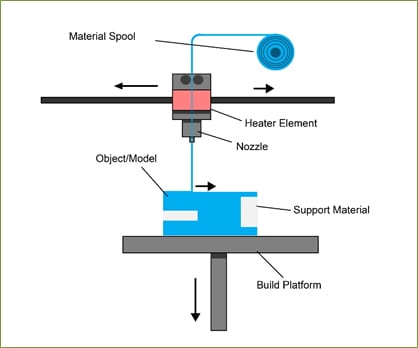
Types of Plastics Used in FDM
The most common printing material for FDM is acrylonitrile butadiene styrene (ABS), a common thermoplastic that’s used to make many consumer products. Along with ABS, some FDM machines also print in other thermoplastics, like polycarbonate (PC) or polyetherimide (PEI). Support materials are usually water-soluble wax or brittle thermoplastics, like polyphenylsulfone (PPSF).
Thermoplastics can endure heat, chemicals and mechanical stress, which makes them an ideal material for printing prototypes that must withstand testing. And because FDM can print highly detailed objects, it’s also commonly used by engineers that need to test parts for fit and form.
0 Comments