Prototype to Production
19
DECEMBER, 2019
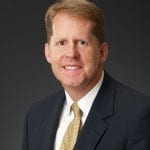
Jeff founded Texas Injection Molding and was the co-founder and Chairman of the Greater Houston Manufacturers Association. Jeff has served two terms as President of the South Texas section of the Society of Plastics Engineers. He is also the co-founder and Director of the Gulf Coast Medical Device Manufacturers and has served on the boards of the Houston Rotary, the University of Houston College of Industrial Engineering and the Houston Community College Advanced Manufacturing Center.
Considering efficient and cost-effective options to bring plastic products to market.
Prototype Production
The ability to develop innovative technology products and efficiently bring them to market has created enormous wealth for America. And America’s innovation will be the key to maintaining its wealth and leadership position in the world.
Those second to market compete on lower margins and live on the coattails of the innovators and entrepreneurs who have led the way. Bringing new technology and new products to market in an efficient and cost-effective method is a key factor in the success of these companies.
For the purpose of this article, I will narrow the focus on identifying the technologies and tooling strategies to bring plastic products to market.
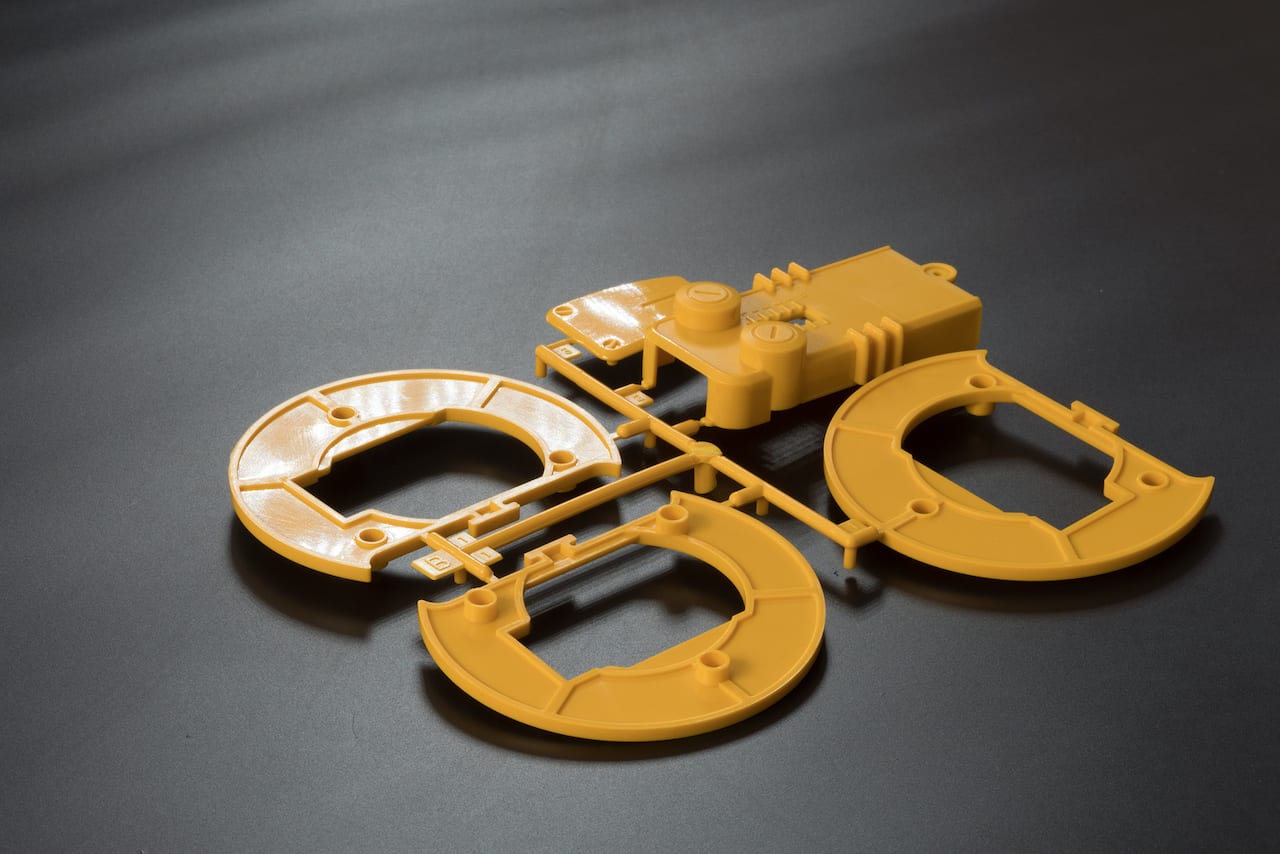
Following the development of a concept to solve a problem or improve a process, it is necessary to prove out the concept with a prototype. The key to a successful prototype is that it represents the critical functions of the final product and provides the ability to test, evaluate, and gain input from users to generate product refinements rapidly.
In the world of plastic products, a prototype may be machined from a solid shape of plastic material, fabricated by combining several components together or printed using additive manufacturing processes. Additive manufacturing, often referred to as 3D Printing, is in the middle of rapid technological advancements.
Early technologies fed a filament through an extruder to selectively place the melted material in X and Y coordinates. Advancements have included UV cured liquid polymers and laser-fused powders offering faster, lower cost, and variety of mechanical and cosmetic attributes. Each respective technology delivers specific characteristics that may be more desirable for testing and evaluating the prototype such as mechanical strength, tactile feel, durability, and cosmetic appearance.
In some instances, the only way to prove out the concept is to prototype with low volume/bridge injection molding tooling. There are innovative new methods using advancements in high-temperature materials that allow additive manufacturing to produce cost-effective cores and cavities to fit in standard size cavities and offer low volume injection molded parts cost-effectively.
To help in your evaluation of technologies we have included comparative attributes of each of the major technologies and videos demonstrating how the technology works on our website.
“The key to a successful prototype is that it represents the critical functions of the final product and provides the ability to test, evaluate, and gain input from users to generate product refinements rapidly.”
For some products that are low volume, machining or additive manufacturing may be the end process.
Technology advancements in additive manufacturing have allowed for printed products to satisfy product performance requirements and cost-effectively satisfy low production volumes without expensive tooling.
I am often asked if additive manufacturing will displace injection molding.
In my opinion, additive manufacturing has dramatically lowered the barriers to entry allowing more ideas to come to market. Yes, additive manufacturing may displace some low volume injection molding and even higher volume in smaller parts that can be printed in an array. However, the volume of injection molding lost to additive manufacturing is far exceeded by the number of new products that are coming to market because of the ease of getting ideas to market that can take advantage of injection molding efficiencies at higher volumes. That is not to say that technology will not someday advance to displace higher volumes or completely disrupt injection molding, but it will not happen overnight.
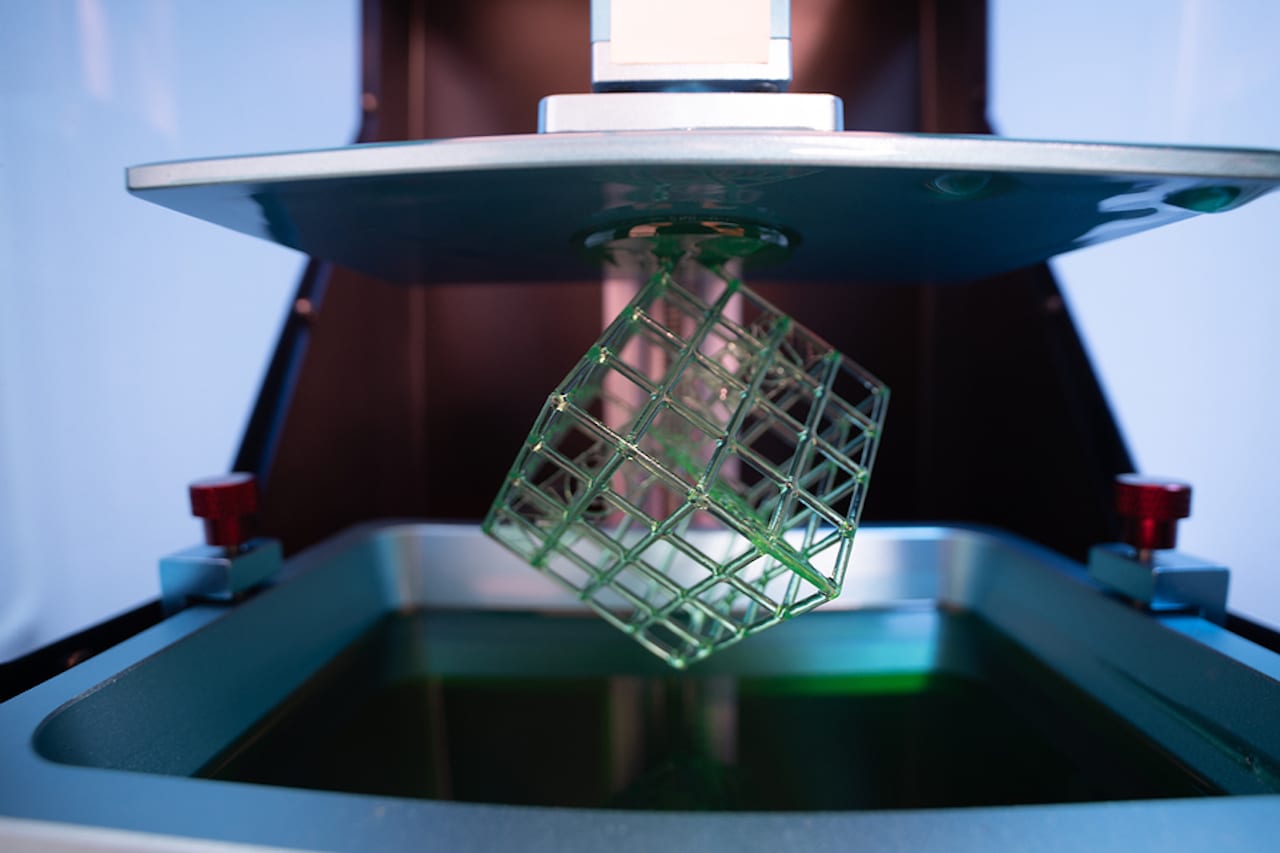
Bridge to Production Tooling
In applications where injection molding offers cost and production capacity advantages it is often appropriate to invest in “bridge to production” tooling. Bridge to production tooling may be appropriate due to some of the following considerations
- Additional testing and evaluation in injection molding thermoplastic material is required to ensure performance to design specifications that can only be achieved by injection molding.
- The market demand is uncertain and preservation of capital is part of the decision to manage risk and return for the new product.
- There are expectations that significant product revisions will emerge post-release of product requiring changes to tooling investment or retooling.
Bridge production tooling often is recognized by single or low cavitation tooling that is created from materials that can be machined or printed faster and at lower cost. Generally, these materials will not stand up to the repeated pressure and fatigue that injection molding will require and may not provide the tolerances or cosmetic specifications of high-volume production tooling.
To help establish construction methods, expectations and standards, The Society of Plastics Industry has issued standards for mold classification. Class 104 and 105 are suitable for prototype and low volume tooling. Class 101, 102 and 103 provide specifications for “production” or very high-volume tooling. More information can be found at this link, SPI Mold Standards.
Production Tooling

Production tooling is designed to deliver high volume, cost effective products that consistently meet the mechanical requirements, cosmetic, quality and environmental performance specifications.
For people not familiar with injection molding, the initial capital cost of production tooling can be surprising.
Each tool is a unique product that is highly engineered for quality and production. In an effort to provide a brief understanding of what constitutes the cost of production tooling I am providing an overview of the construction of production tooling.
- Mold Base – The mold base is the foundation of the tool. It is engineered to contain the mold and withstand the high pressures expected during molding. The outer steel plates are used to clamp the mold into the press. The mold base contains the ejector box and plate used to eject parts from the cavity. Support pillars are often engineered to support the load that injection pressure will apply while filling the cavity to ensure that the steel will not flex. Depending on the part design, the mold may contain hydraulic systems or large pins to move sections of steel to clear undercuts as the mold opens and closes.
- Core and Cavity – The core and cavity are the two halves of the mold that contain the geometry of the part and is where the part is formed. Dimensions are engineered to ensure that material shrinkage during cooling is considered. Part geometry of one or multiple cores and cavities is machined and finished with texture and polish specifications. Polishing to specified finishes is often done by hand to SPI Mold Polish Specifications.
- Ejection system – The mold base allows for a steel plate to move forward pushing core pins into specified areas of the cavity to push the finished part out after molding is completed. There are multiple pins that are ground to exact length for each cavity to push the part out with minimal witness marks.
- Cooling system – After the part is formed by injecting the melted thermoplastic resin into the cavity, water lines are engineered and drilled in the steel to provide balanced and efficient cooling.
-
Runner systems are designed to create a path for the resin to flow into the cavities. There are many different types of runner systems that significantly impact the cost and performance of the mold.
- A cold runner feeds resin from the molding machine to the cavity but must be removed from the part. This can be captured, ground and reintroduced to the virgin material.
- A hot sprue will incorporate heaters within the mold to maintain a constant temperature of the melted plastic material to minimize the volume of cold runner that needs to be captured, reground and reused. Typically, a short length that represents a small percentage of runner will remain that can be reused or discarded.
- A hot runner manifold with hot tips maintain the temperature all the way to the wall of the part and may incorporate a valve to minimize the cosmetic effect of the injection point on the part and eliminate any additional runner that would need to be handled and reused. Depending on the number of drops and complexity of hot runner system engineered into the tool, the cost of the hot runner and hot tip can be in the tens of thousands of dollars and greater.
- Other options: Considering every part design is unique and has different geometry, volume considerations, texture, materials, tolerances, quality and cosmetic requirements; there are a variety of options and additional engineered solutions that impact tool cost.
I hope this gives a general overview of options and cost considerations for taking your project from prototype to production. More information and resources can be found on our websites Texas Prototype and Texas Injection Molding along with contact information where one of our engineers can help you.


0 Comments